一、何谓原料仓
原料仓:指的是在矿山井底、选料厂、电厂、焦化厂等地面进行临时贮存物料的场所,在生产过程中,主要是用于放置原料的容器。在款山井下的小型原料仓主要是起到缓冲仓的作用,大型料仓主要是起到仓储作用。原料仓终归是用于中转物料的作用,拥有物料的输入口和输出口,确保原料仓的正常运转,是矿山生产、运输、存储等环节的重中之重!
二、为何研究原料仓
中矿冶金科技有限公司的研发团队,下大力气对全国大范围内料仓开展研究,深入矿山井下及众多选料厂、电厂、焦化厂的料仓现场进行大量的实地研究。主要基于以下三点原因:
1、料仓数量众多,涉及面极广;
2、料仓在生产、运输、存储等环节作用巨大;
3、料仓事故频发,造成损失巨大。
三、指导原则
1、解决根本性问题,从源头抓起。
俗话说“病从口入”,要想解决料仓的一系列问题,必须解决原料的来源问题,从跟不上解决料仓问题。
2、做好料仓防护工作,杜绝事故的发生。
当出现应急情况的时候,必须有预先设计好的应急措施,以备不测,防止事故的发生。
3、综合治理,解决多种难题
料仓的难题是多样性、复杂性,必须打出组合拳,多方位武装料仓。切不可脚疼医脚、手疼医手,只是解决局部难题。
四、料仓面临的重大问题
在日常生产的过程中,原料仓主要面临以下三大难题:
1、堵仓 90%以上的原料仓都发生过堵塞问题,造成堵仓的主要原因有以下几种情况:
①料粒结块
料块自身之间,料块与筒壁之间的摩擦力也越来越大,料块之间发生团聚,特征尺寸显著增大,堵塞在内径较小处,容易造成料块结构性堵仓。
②粘料
原料粘性大,自身容易积聚,同时与仓壁形成黏结,在生产过程中,粘料造成的堵仓事故比例非常高。
③大渣石、大料块卡堵
大块渣石、大料块流通到仓口的时候,非常容易造成堵仓,直接锁住仓口,动弹不得,造成严重堵仓。
④杂物裹挟
从采料面、掘进面过来的锚杆、枕木、型钢、金属网等杂物,落入料仓,非常容易造成堵仓。
⑤料仓内存料太少
当料仓存料太较少时,料块从高空向底部加速度冲击,冲击力非常大,底部少量存料被冲击压实,再次放料时候,就容易结块造成堵塞。
⑥料仓混凝土仓壁表面粗糙,摩擦系数大。这是料仓内部出现了自身问题,内部凸凹不平,甚至渗水,物料堆聚,容易造成堵仓。
⑦料仓结构问题
料仓结构非常关键,出口太小,底部收口为方锥,流通截面突然变小,这从根本上容易造成堵仓。
2、窜仓(也称涌仓、溃仓)
综采工作面生产时,顺槽皮带将水及料运输至中转料仓,水料由此在仓内堆积,当料仓出口给料机启动,料水混合物一涌而出,容易发生窜仓事故。另外当料仓出现粘料堵仓的时候,为了疏通料仓,人工采用高压水枪向料仓内注水,形成水料浆,当料仓瞬间疏通后,料水混合物快速流通,同样容易出现窜仓事故。窜仓造成的危害是巨大的,严重的造成设备损坏、巷道堵塞、甚至是人员伤亡,并直接造成生产停滞。
综上所述:造成窜仓的直接原因,就是大量水料在料仓内形成了容易快速流通的水料浆!
3、蓬仓
当料块较多落入时内阻力增大,料块容易在料仓内径较小处堆积、“搭桥”也就是“蓬料”。
近壁料粒是滑动摩擦力较大的料粒与料粒间的相对运动,不是滑动摩擦力较小的料粒与光滑仓壁间的相对运动,近壁料粒处于滞流状态。近壁料粒越长时间滞流越容易被压实,越使料粒与料粒间以及料粒与光滑仓壁间的静摩擦力增大,也就是说这部分近壁料粒越容易滞流不动而贴壁生根。
在中间区域料粒流经贴壁生根料粒过程中,若流动料粒的重力小于料粒与料粒间的滑动摩擦力时,流动料粒将粘附到贴壁生根料粒上而静止不动,随着时间的推移,料粒与料粒间的静摩擦力不断增大,静止料粒逐渐成为了生根料粒。由于生根料粒的不断增高增厚,蓬料状态也就形成了。有两种情况最容易形成蓬仓:
①大块渣石、料块、长条状杂物进入料仓后,在料仓出口或者与仓壁搭接,非常容易出现蓬仓现象。
②粘料的出现,其与仓壁容易形成拱型搭桥,造成蓬仓现象。
五、料仓的硬性规定
1、根据2016版《煤矿安全规程》133条规定: 倾角在25°以上的小眼、煤仓、溜煤(矸)眼、 人行道、上山和下山的上口、必须设防止人员、物料坠落的设施。
2、根据2016版《煤矿安全规程》134条规定:煤仓、溜煤(矸)眼必须有防止溜煤(矸)堵塞的设施。检查煤仓、溜煤(矸)眼和处理堵塞时,必须制定安全措施。处理堵塞时应当遵守本规程第三百六十条的规定,严禁人员从下方进入。严禁煤仓、溜煤(矸)眼兼做流水道。煤仓与溜煤(矸)眼内有淋水时,必须采取封堵疏干措施;没有得到妥善处理不得使用。
3、根据2016版《煤矿安全规程》151条规定:井下所有煤仓和溜煤眼都应当保持一定的存煤,不得放空;有涌水的煤仓和溜煤眼,可以放空,但放空后放煤口闸板必须关闭,并设置引水管。溜煤眼不得兼作风眼使用。
4、根据2016版《煤矿安全规程》423条规定:提升装置必须按照下列要求装设安全保护 (八)仓位超限保护:箕斗提升的井口煤仓仓位超限时,能报警并闭锁开车。
5、根据2016版《煤矿安全规程》499条规定:井下下列地点必须设置甲烷传感器: (七)煤仓上方、封闭的带式输送机地面走廊。
6、根据2016版《煤矿安全规程》643条规定:粉尘监测采样点布置:地面作业场所,地面煤仓;测尘点布置,作业人员活动范围内。
7、根据2016版《煤矿安全规程》644条规定:矿井必须建立消防防尘供水系统,并遵守下列规定:煤仓放煤口、溜煤眼放煤口、卸载点等地点必须敷设防尘供水管路,并安设支管和阀门。防尘用水应当过滤。
8、根据2016版《煤矿安全规程》652条规定:井下煤仓 (溜煤眼)放煤口、输送机转载点和卸载点,以及地面筛分厂、破碎车间、带式输送机走廊、转载点等地点,必须安设喷雾装置或者除尘器,作业时进行喷雾降尘或者用除尘器除尘。
六、原煤仓事故案例
1、2019年12月29日凌晨,大同煤矿集团地煤公司焦煤矿305煤眼发生一起流煤眼歘煤事故,事发当时被困6人,经矿积极组织抢险救援,其中1人送医后生命体征平稳,5人经抢救无效死亡。煤仓残存煤矸泥蓬仓于下锁口;煤仓上口巷道裂隙水流入煤仓,埋下隐患;违规启动煤仓给煤机,造成约84立方米水煤瞬间窜仓,水煤浆造成的窜仓是造成本次事故的直接原因。
2、2019年10月21日22时,锦运煤矿,主斜井下部车场煤仓,根据工作安排,当班人员对主斜井下部车场煤仓内淤积的原煤进行清理,为加快清理速度、清理工就下到煤仓底部,由下往上清理,次日7时35分,因淤积煤炭的下部被掏空,仓壁上方的原煤沿煤仓壁快速下滑,将清理工冲倒并掩埋,清理煤仓底部淤积造成仓壁沿煤下滑是本次事故的直接原因。
3、2009年1月8日凌晨5:04分,袁庄矿Ⅳ1采区集运机头煤仓发生一起皮带机司机坠入煤仓致死事故。2009年1月7日夜班,皮带机司机没有按照透眼措施规定汇报值班人员,而是自己翻过安全护栏,站在溜煤道上口进行直接透眼,不慎由溜煤道坠入井下煤仓内,后经抢救无效死亡。现场安全措施落实不到位。栅栏没有全封闭、煤仓上口没有保险带。没有安全措施的情况下透眼是本次坠入煤仓事故的直接原因。
4、2009年6月16日19时左右,庞庞塔矿工人在主斜井强力皮带机尾清理浮煤,主井底原煤仓出口给煤机的闸门没有到位,水煤开始下落,不一会突然发生水煤窜仓,大量水煤窜至皮带机尾,将在此清理浮煤的3个工人掩埋, 造成主斜井末端横贯堵塞,机尾被埋,三人死亡。水煤涌进煤仓,导致煤仓结拱,结拱突然坍塌造成窜仓是本次事故的直接原因。
5、2001年4月22日早晨,晓南矿中央胶带输送机道煤仓,倒仓队安排白班清中央胶带输送机道缓冲煤仓,班前会上比较认真地贯彻了措施。11时10分清仓工系安全带进入煤仓,11时38分左右向仓上口喊话,要求关闭压风,并向下仓口喊话要求停胶带输送机,在胶带输送机停机瞬间发生了仓壁浮煤坠落,将清仓工埋住。经过矿积极组织抢救,16时将清仓工从煤仓中扒出,已死亡。在清理煤仓过程中浮煤坠落是造成本次事故的直接原因。
6、2014年4月10日,刘家梁煤矿主井底原煤仓发生第一次窜仓后,安排工人在定量斗平台上清理窜仓遗留的煤泥,主井底原煤仓持续渗水使仓壁上残存的煤泥突然滑落,造成二次窜仓,水煤浆从给煤机出口快速通过,直接将在定量斗平台上清理煤泥的3个工人冲下平台,坠入井底,造成人员伤亡。二次窜仓是造成本次事故的直接原因。
7、2015年11月17日,张家口发电厂4号锅炉原煤仓,中标单位工人对4号煤仓进行内部清拱,在清煤的过程中,仓内上部侧壁存煤突然坍塌,将清理工埋入煤下。事故发生后,经全力抢救无效清理工死亡。按照规定:煤仓内积煤粘在仓壁上而仓内余煤量不大时,从进人口挂好爬梯进入,从上而下依次将粘壁原煤清理下,使其自然流至锥形斗下煤口处。清理人员站在有浮煤的下方清理,造成仓壁粘煤松动,仓壁粘煤坍塌是造成本次事故的直接原因。
8、2011年7月8日,沙曲矿南胶1#煤仓,皮带队副队长发现南胶1#煤仓被堵仓,经现场实际勘查后,发现煤仓内被大矸石拥挤后卡住造成堵仓,大矸石来源:综采一队15101工作面顶板破碎,采煤机割煤及支架拉移过程中,将大块矸石跌落到运输机内将其运出,工作面的破碎机不能正常开启,导致大矸石从工作面被运输进入煤仓。大矸石没有被发现并破碎是造成本次堵仓的直接原因。
9、望峰岗选煤厂经过2006年改扩建后,拥有4个原煤仓,煤仓直径22m,高47m,最大原煤存储量1万t,由于原煤仓内的瓦斯浓度高达4.2%,瓦斯含量过高,加之该选煤厂的原煤仓内部曾发生过瓦斯自燃事故,为消灭潜在事故,遂决定向原煤仓内喷水,造成原煤仓发生窜仓,约150t水煤浆自煤仓出口瞬间倾泻而出,直接将煤仓下方的给煤机、运输机覆盖,造成设备损坏;向煤仓喷水形成水煤浆是造成本次窜仓的直接原因。
10、2011年9月3日夜班,碱沟煤矿东三+495煤仓,煤仓口西帮一根Φ50的PVC供水管从接头处断开,一股水流直接冲到石门水沟,石门水沟溢满后又流入煤仓;在东三+541m下山绕道处找到闸阀并关闭闸阀,由于闸阀锈蚀严重,无法将阀完全关死,水不能及时关掉,诱发了窜仓事故的扩大。Φ50的PVC供水管接头处质量存在问题,承压强度不够,从接头处断开,水流进入煤仓是造成本次窜仓事故发生的直接原因。
11、2005年11月23日零点班,常村矿主井提煤时箕斗提不动,派人检查后发现箕斗超重,派人检查,发现井底水窝溜煤口堵死,水窝流入大量煤约300吨,调派人员在溜煤口下方斜巷进行清理。下午5时左右正在清理积煤,突然从溜煤口处涌出大量水煤,将一名职工埋在煤里,周围的人员立即组织去抢救,这时又有大量水煤涌出,又把两名职工埋在煤里,造成3名职工不幸遇难的较大事故。主井提升系统对装载站多装载故障没有显示,控制程序存在问题,是这次事故的源头。现场箕斗发生二次装载、多次装载没有被及时发现,水煤造成的窜仓是本次事故的直接原因。
12、1987年9月1日,阳泉矿务局四矿二区四尺煤31区煤仓,煤仓发生篷仓,入仓皮带停止运行。区领导要求煤仓上口岗位工往煤仓里注水,想用水将篷煤冲下,先后进行了6次灌水,灌水量总计205.39立方米。2日16时左右,维运区副区长用大锤敲打扇形门的连杆,又用撬棍在摇动板变形处的小口捅煤,正在处理当中,突然听到给煤机上有响声,生产副矿长在平台上发现东、西两侧箱板都有不同程度的裂缝和开焊,其他7人便从煤仓下往北撤离,突然一声轰鸣,水煤泥从煤仓口窜仓,其中6人在仓北6.4—23米的位置被煤泥流掩埋死亡。事故发生后经调查测定,冲出煤泥水合计573立方米,煤泥水淤积巷道210米(煤仓南侧90米,北侧210米)。蓬仓后向仓内大量灌水,超过了给煤机箱板两侧的承载能力。向煤仓灌水引发窜仓是造成本次事故的直接原因。
13、2005年11月27日21时22分,龙煤集团有限责任公司七台河分公司东风煤矿,该矿井口煤仓堵塞,现场人员使用炸药爆破疏通方式,进行煤仓疏通。使用炸药爆破疏通方式,引起粉尘爆炸事故,导致煤尘飞扬达到爆炸界限,放炮火焰穿到井下煤尘爆炸的一起重大的责任事故,事故调查最后死亡171人,伤48人,直接经济损失4293.1万。使用非专用炸药违章作业处理煤仓堵塞是造成这次特重大事故发生的直接原因。
14、2017年10月26日0时,淮南矿业集团潘二煤矿在西二采区煤仓内进行修护作业时,西二采区煤仓中部锚(杆)喷支护段片帮垮落后,锚杆、金属网、湿煤及大块矸石等混在一起,导致煤仓内煤矸局部堆积不实,维护工站在堆积不实的煤矸平台上作业时,佩戴的保险带未固定在预留的保险绳上,煤矸突然塌陷,维护工随之陷落被埋致死。在煤仓内煤矸平台上作业时,仓壁片帮突然塌落造成本次事故的直接原因。
15、1998年10月5日白班,大兴矿对地面圆筒储煤仓进行清仓。救护队现场勘查1号放煤口货量较少,便确定由1号放煤仓上人检查仓内情况并形成上人台阶。准备攀上分煤器上部清货,煤仓分煤器挂货突然片帮,紧接又连续两次片帮掉货,将煤仓清理人埋住,虽经在场的救护队职工奋力抢救,但因抢救无效死亡。自下而上清理煤仓,分煤器挂煤洒落是造成本次事故的直接原因。
七、解决方案
综上所述,我们可以总结到料仓在日常运行的过程中,遇到的难题是丛出不穷的,造成的事故更是普遍的,危害性极大,给现场操作人员及管理人员带来了众多障碍。
如何去解决料仓的难题?八仙过海,日积月累,现场广大职工也都想尽了办法。具体有:大锤振、撬棍捅、风镐砸、高压水枪冲、放炮崩、空气炮、疏松机等等。
以上所有方法都有两个共性:
其一是:局部性,现场各个单位根据自身料仓遇到的问题,采取临时的局部应急措施。在某种程度上解决了现场临时的问题,但对于整个行业来说,并没有形成一套完整的解决方案。
其二是:被动性,以上料仓事故处理的所有方法,全部是因料仓形成既有事故后开展实施的,没有前瞻性和预见性。
中矿冶金科技有限公司研发团队通过现场大量的调研总结,就是要在行业内形成一套解决料仓难题的产品体系,从根本上解决料仓所遇到的种种难题,而不是拘泥于某一个料仓的问题。
中矿冶金科技有限公司研发的料仓智能运行系统具有显著的自身特征:
其一是:综合性,根据料仓容易发生堵仓、窜仓、蓬仓等事故,综合治理,标本兼治,形成一套完整的产品体系。
其二是:主动性,从原料来源入手,在原料入仓之前,对原料进行有效处理,防止料仓事故发生。
其三是:智能性,在料仓运行系统中置入图像智能识别技术,通过软件建立数据库,使系统具有自学习能力,替代人工监测。
八、项目重大意义
目前现场运行的料仓数量庞大,事故发生非常频繁,给生产及人身安全造成重大损失,中矿冶金科技有限公司研发的料仓智能运行系统产生了良好的经济价值和社会价值,具有很强的推广应用价值。
具体如下:
1、确保原料仓的正常运转;
2、避免料仓灾害事故的发生;
3、提高现场工作人员的管理水平;
4、为行业树立新的标杆及标准。
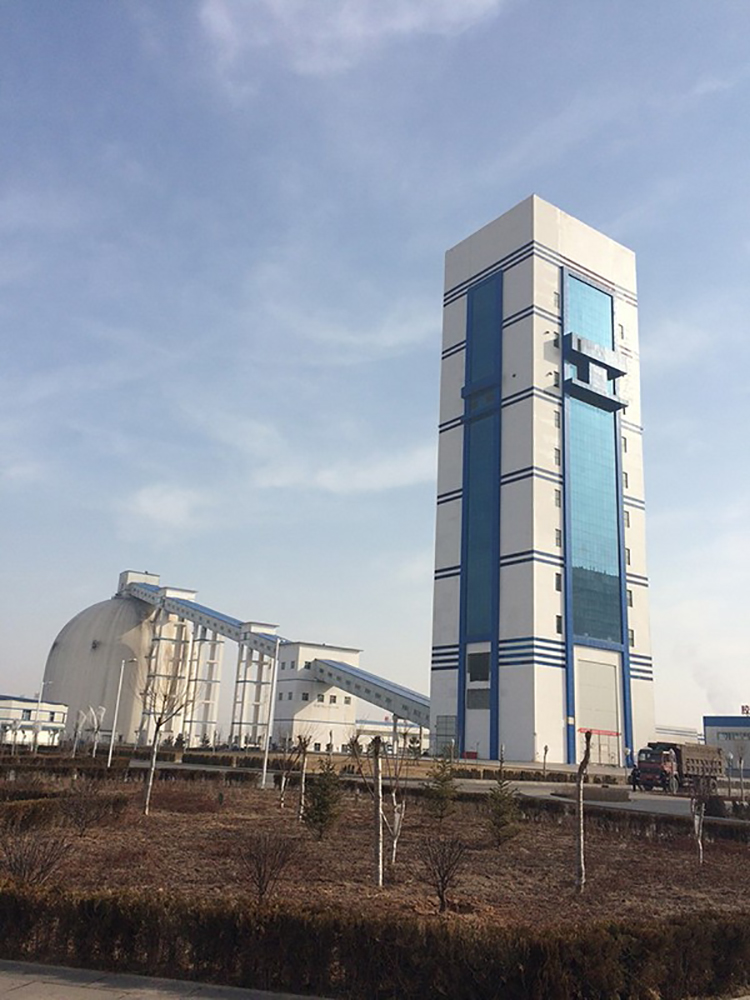
原料仓:指的是在矿山井底、选料厂、电厂、焦化厂等地面进行临时贮存物料的场所,在生产过程中,主要是用于放置原料的容器。在款山井下的小型原料仓主要是起到缓冲仓的作用,大型料仓主要是起到仓储作用。原料仓终归是用于中转物料的作用,拥有物料的输入口和输出口,确保原料仓的正常运转,是矿山生产、运输、存储等环节的重中之重!
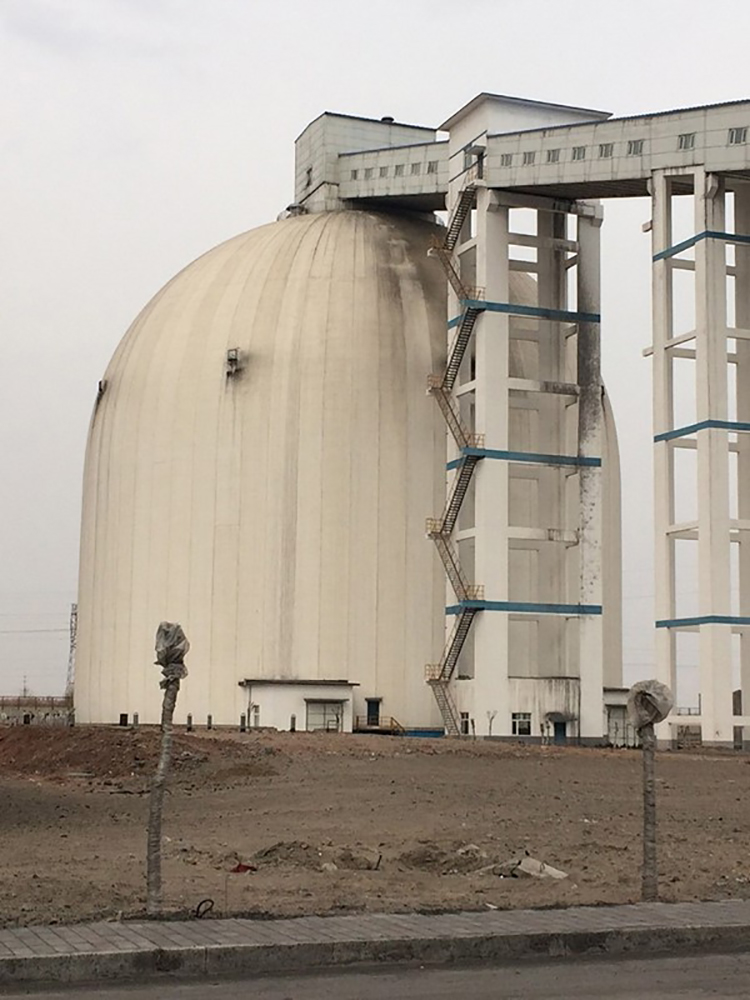
二、为何研究原料仓
中矿冶金科技有限公司的研发团队,下大力气对全国大范围内料仓开展研究,深入矿山井下及众多选料厂、电厂、焦化厂的料仓现场进行大量的实地研究。主要基于以下三点原因:
1、料仓数量众多,涉及面极广;
2、料仓在生产、运输、存储等环节作用巨大;
3、料仓事故频发,造成损失巨大。
三、指导原则
1、解决根本性问题,从源头抓起。
俗话说“病从口入”,要想解决料仓的一系列问题,必须解决原料的来源问题,从跟不上解决料仓问题。
2、做好料仓防护工作,杜绝事故的发生。
当出现应急情况的时候,必须有预先设计好的应急措施,以备不测,防止事故的发生。
3、综合治理,解决多种难题
料仓的难题是多样性、复杂性,必须打出组合拳,多方位武装料仓。切不可脚疼医脚、手疼医手,只是解决局部难题。
四、料仓面临的重大问题
在日常生产的过程中,原料仓主要面临以下三大难题:
1、堵仓 90%以上的原料仓都发生过堵塞问题,造成堵仓的主要原因有以下几种情况:
①料粒结块
料块自身之间,料块与筒壁之间的摩擦力也越来越大,料块之间发生团聚,特征尺寸显著增大,堵塞在内径较小处,容易造成料块结构性堵仓。
②粘料
原料粘性大,自身容易积聚,同时与仓壁形成黏结,在生产过程中,粘料造成的堵仓事故比例非常高。
③大渣石、大料块卡堵
大块渣石、大料块流通到仓口的时候,非常容易造成堵仓,直接锁住仓口,动弹不得,造成严重堵仓。
④杂物裹挟
从采料面、掘进面过来的锚杆、枕木、型钢、金属网等杂物,落入料仓,非常容易造成堵仓。
⑤料仓内存料太少
当料仓存料太较少时,料块从高空向底部加速度冲击,冲击力非常大,底部少量存料被冲击压实,再次放料时候,就容易结块造成堵塞。
⑥料仓混凝土仓壁表面粗糙,摩擦系数大。这是料仓内部出现了自身问题,内部凸凹不平,甚至渗水,物料堆聚,容易造成堵仓。
⑦料仓结构问题
料仓结构非常关键,出口太小,底部收口为方锥,流通截面突然变小,这从根本上容易造成堵仓。
2、窜仓(也称涌仓、溃仓)
综采工作面生产时,顺槽皮带将水及料运输至中转料仓,水料由此在仓内堆积,当料仓出口给料机启动,料水混合物一涌而出,容易发生窜仓事故。另外当料仓出现粘料堵仓的时候,为了疏通料仓,人工采用高压水枪向料仓内注水,形成水料浆,当料仓瞬间疏通后,料水混合物快速流通,同样容易出现窜仓事故。窜仓造成的危害是巨大的,严重的造成设备损坏、巷道堵塞、甚至是人员伤亡,并直接造成生产停滞。
综上所述:造成窜仓的直接原因,就是大量水料在料仓内形成了容易快速流通的水料浆!
3、蓬仓
当料块较多落入时内阻力增大,料块容易在料仓内径较小处堆积、“搭桥”也就是“蓬料”。
近壁料粒是滑动摩擦力较大的料粒与料粒间的相对运动,不是滑动摩擦力较小的料粒与光滑仓壁间的相对运动,近壁料粒处于滞流状态。近壁料粒越长时间滞流越容易被压实,越使料粒与料粒间以及料粒与光滑仓壁间的静摩擦力增大,也就是说这部分近壁料粒越容易滞流不动而贴壁生根。
在中间区域料粒流经贴壁生根料粒过程中,若流动料粒的重力小于料粒与料粒间的滑动摩擦力时,流动料粒将粘附到贴壁生根料粒上而静止不动,随着时间的推移,料粒与料粒间的静摩擦力不断增大,静止料粒逐渐成为了生根料粒。由于生根料粒的不断增高增厚,蓬料状态也就形成了。有两种情况最容易形成蓬仓:
①大块渣石、料块、长条状杂物进入料仓后,在料仓出口或者与仓壁搭接,非常容易出现蓬仓现象。
②粘料的出现,其与仓壁容易形成拱型搭桥,造成蓬仓现象。
五、料仓的硬性规定
1、根据2016版《煤矿安全规程》133条规定: 倾角在25°以上的小眼、煤仓、溜煤(矸)眼、 人行道、上山和下山的上口、必须设防止人员、物料坠落的设施。
2、根据2016版《煤矿安全规程》134条规定:煤仓、溜煤(矸)眼必须有防止溜煤(矸)堵塞的设施。检查煤仓、溜煤(矸)眼和处理堵塞时,必须制定安全措施。处理堵塞时应当遵守本规程第三百六十条的规定,严禁人员从下方进入。严禁煤仓、溜煤(矸)眼兼做流水道。煤仓与溜煤(矸)眼内有淋水时,必须采取封堵疏干措施;没有得到妥善处理不得使用。
3、根据2016版《煤矿安全规程》151条规定:井下所有煤仓和溜煤眼都应当保持一定的存煤,不得放空;有涌水的煤仓和溜煤眼,可以放空,但放空后放煤口闸板必须关闭,并设置引水管。溜煤眼不得兼作风眼使用。
4、根据2016版《煤矿安全规程》423条规定:提升装置必须按照下列要求装设安全保护 (八)仓位超限保护:箕斗提升的井口煤仓仓位超限时,能报警并闭锁开车。
5、根据2016版《煤矿安全规程》499条规定:井下下列地点必须设置甲烷传感器: (七)煤仓上方、封闭的带式输送机地面走廊。
6、根据2016版《煤矿安全规程》643条规定:粉尘监测采样点布置:地面作业场所,地面煤仓;测尘点布置,作业人员活动范围内。
7、根据2016版《煤矿安全规程》644条规定:矿井必须建立消防防尘供水系统,并遵守下列规定:煤仓放煤口、溜煤眼放煤口、卸载点等地点必须敷设防尘供水管路,并安设支管和阀门。防尘用水应当过滤。
8、根据2016版《煤矿安全规程》652条规定:井下煤仓 (溜煤眼)放煤口、输送机转载点和卸载点,以及地面筛分厂、破碎车间、带式输送机走廊、转载点等地点,必须安设喷雾装置或者除尘器,作业时进行喷雾降尘或者用除尘器除尘。
六、原煤仓事故案例
1、2019年12月29日凌晨,大同煤矿集团地煤公司焦煤矿305煤眼发生一起流煤眼歘煤事故,事发当时被困6人,经矿积极组织抢险救援,其中1人送医后生命体征平稳,5人经抢救无效死亡。煤仓残存煤矸泥蓬仓于下锁口;煤仓上口巷道裂隙水流入煤仓,埋下隐患;违规启动煤仓给煤机,造成约84立方米水煤瞬间窜仓,水煤浆造成的窜仓是造成本次事故的直接原因。
2、2019年10月21日22时,锦运煤矿,主斜井下部车场煤仓,根据工作安排,当班人员对主斜井下部车场煤仓内淤积的原煤进行清理,为加快清理速度、清理工就下到煤仓底部,由下往上清理,次日7时35分,因淤积煤炭的下部被掏空,仓壁上方的原煤沿煤仓壁快速下滑,将清理工冲倒并掩埋,清理煤仓底部淤积造成仓壁沿煤下滑是本次事故的直接原因。
3、2009年1月8日凌晨5:04分,袁庄矿Ⅳ1采区集运机头煤仓发生一起皮带机司机坠入煤仓致死事故。2009年1月7日夜班,皮带机司机没有按照透眼措施规定汇报值班人员,而是自己翻过安全护栏,站在溜煤道上口进行直接透眼,不慎由溜煤道坠入井下煤仓内,后经抢救无效死亡。现场安全措施落实不到位。栅栏没有全封闭、煤仓上口没有保险带。没有安全措施的情况下透眼是本次坠入煤仓事故的直接原因。
4、2009年6月16日19时左右,庞庞塔矿工人在主斜井强力皮带机尾清理浮煤,主井底原煤仓出口给煤机的闸门没有到位,水煤开始下落,不一会突然发生水煤窜仓,大量水煤窜至皮带机尾,将在此清理浮煤的3个工人掩埋, 造成主斜井末端横贯堵塞,机尾被埋,三人死亡。水煤涌进煤仓,导致煤仓结拱,结拱突然坍塌造成窜仓是本次事故的直接原因。
5、2001年4月22日早晨,晓南矿中央胶带输送机道煤仓,倒仓队安排白班清中央胶带输送机道缓冲煤仓,班前会上比较认真地贯彻了措施。11时10分清仓工系安全带进入煤仓,11时38分左右向仓上口喊话,要求关闭压风,并向下仓口喊话要求停胶带输送机,在胶带输送机停机瞬间发生了仓壁浮煤坠落,将清仓工埋住。经过矿积极组织抢救,16时将清仓工从煤仓中扒出,已死亡。在清理煤仓过程中浮煤坠落是造成本次事故的直接原因。
6、2014年4月10日,刘家梁煤矿主井底原煤仓发生第一次窜仓后,安排工人在定量斗平台上清理窜仓遗留的煤泥,主井底原煤仓持续渗水使仓壁上残存的煤泥突然滑落,造成二次窜仓,水煤浆从给煤机出口快速通过,直接将在定量斗平台上清理煤泥的3个工人冲下平台,坠入井底,造成人员伤亡。二次窜仓是造成本次事故的直接原因。
7、2015年11月17日,张家口发电厂4号锅炉原煤仓,中标单位工人对4号煤仓进行内部清拱,在清煤的过程中,仓内上部侧壁存煤突然坍塌,将清理工埋入煤下。事故发生后,经全力抢救无效清理工死亡。按照规定:煤仓内积煤粘在仓壁上而仓内余煤量不大时,从进人口挂好爬梯进入,从上而下依次将粘壁原煤清理下,使其自然流至锥形斗下煤口处。清理人员站在有浮煤的下方清理,造成仓壁粘煤松动,仓壁粘煤坍塌是造成本次事故的直接原因。
8、2011年7月8日,沙曲矿南胶1#煤仓,皮带队副队长发现南胶1#煤仓被堵仓,经现场实际勘查后,发现煤仓内被大矸石拥挤后卡住造成堵仓,大矸石来源:综采一队15101工作面顶板破碎,采煤机割煤及支架拉移过程中,将大块矸石跌落到运输机内将其运出,工作面的破碎机不能正常开启,导致大矸石从工作面被运输进入煤仓。大矸石没有被发现并破碎是造成本次堵仓的直接原因。
9、望峰岗选煤厂经过2006年改扩建后,拥有4个原煤仓,煤仓直径22m,高47m,最大原煤存储量1万t,由于原煤仓内的瓦斯浓度高达4.2%,瓦斯含量过高,加之该选煤厂的原煤仓内部曾发生过瓦斯自燃事故,为消灭潜在事故,遂决定向原煤仓内喷水,造成原煤仓发生窜仓,约150t水煤浆自煤仓出口瞬间倾泻而出,直接将煤仓下方的给煤机、运输机覆盖,造成设备损坏;向煤仓喷水形成水煤浆是造成本次窜仓的直接原因。
10、2011年9月3日夜班,碱沟煤矿东三+495煤仓,煤仓口西帮一根Φ50的PVC供水管从接头处断开,一股水流直接冲到石门水沟,石门水沟溢满后又流入煤仓;在东三+541m下山绕道处找到闸阀并关闭闸阀,由于闸阀锈蚀严重,无法将阀完全关死,水不能及时关掉,诱发了窜仓事故的扩大。Φ50的PVC供水管接头处质量存在问题,承压强度不够,从接头处断开,水流进入煤仓是造成本次窜仓事故发生的直接原因。
11、2005年11月23日零点班,常村矿主井提煤时箕斗提不动,派人检查后发现箕斗超重,派人检查,发现井底水窝溜煤口堵死,水窝流入大量煤约300吨,调派人员在溜煤口下方斜巷进行清理。下午5时左右正在清理积煤,突然从溜煤口处涌出大量水煤,将一名职工埋在煤里,周围的人员立即组织去抢救,这时又有大量水煤涌出,又把两名职工埋在煤里,造成3名职工不幸遇难的较大事故。主井提升系统对装载站多装载故障没有显示,控制程序存在问题,是这次事故的源头。现场箕斗发生二次装载、多次装载没有被及时发现,水煤造成的窜仓是本次事故的直接原因。
12、1987年9月1日,阳泉矿务局四矿二区四尺煤31区煤仓,煤仓发生篷仓,入仓皮带停止运行。区领导要求煤仓上口岗位工往煤仓里注水,想用水将篷煤冲下,先后进行了6次灌水,灌水量总计205.39立方米。2日16时左右,维运区副区长用大锤敲打扇形门的连杆,又用撬棍在摇动板变形处的小口捅煤,正在处理当中,突然听到给煤机上有响声,生产副矿长在平台上发现东、西两侧箱板都有不同程度的裂缝和开焊,其他7人便从煤仓下往北撤离,突然一声轰鸣,水煤泥从煤仓口窜仓,其中6人在仓北6.4—23米的位置被煤泥流掩埋死亡。事故发生后经调查测定,冲出煤泥水合计573立方米,煤泥水淤积巷道210米(煤仓南侧90米,北侧210米)。蓬仓后向仓内大量灌水,超过了给煤机箱板两侧的承载能力。向煤仓灌水引发窜仓是造成本次事故的直接原因。
13、2005年11月27日21时22分,龙煤集团有限责任公司七台河分公司东风煤矿,该矿井口煤仓堵塞,现场人员使用炸药爆破疏通方式,进行煤仓疏通。使用炸药爆破疏通方式,引起粉尘爆炸事故,导致煤尘飞扬达到爆炸界限,放炮火焰穿到井下煤尘爆炸的一起重大的责任事故,事故调查最后死亡171人,伤48人,直接经济损失4293.1万。使用非专用炸药违章作业处理煤仓堵塞是造成这次特重大事故发生的直接原因。
14、2017年10月26日0时,淮南矿业集团潘二煤矿在西二采区煤仓内进行修护作业时,西二采区煤仓中部锚(杆)喷支护段片帮垮落后,锚杆、金属网、湿煤及大块矸石等混在一起,导致煤仓内煤矸局部堆积不实,维护工站在堆积不实的煤矸平台上作业时,佩戴的保险带未固定在预留的保险绳上,煤矸突然塌陷,维护工随之陷落被埋致死。在煤仓内煤矸平台上作业时,仓壁片帮突然塌落造成本次事故的直接原因。
15、1998年10月5日白班,大兴矿对地面圆筒储煤仓进行清仓。救护队现场勘查1号放煤口货量较少,便确定由1号放煤仓上人检查仓内情况并形成上人台阶。准备攀上分煤器上部清货,煤仓分煤器挂货突然片帮,紧接又连续两次片帮掉货,将煤仓清理人埋住,虽经在场的救护队职工奋力抢救,但因抢救无效死亡。自下而上清理煤仓,分煤器挂煤洒落是造成本次事故的直接原因。
七、解决方案
综上所述,我们可以总结到料仓在日常运行的过程中,遇到的难题是丛出不穷的,造成的事故更是普遍的,危害性极大,给现场操作人员及管理人员带来了众多障碍。
如何去解决料仓的难题?八仙过海,日积月累,现场广大职工也都想尽了办法。具体有:大锤振、撬棍捅、风镐砸、高压水枪冲、放炮崩、空气炮、疏松机等等。
以上所有方法都有两个共性:
其一是:局部性,现场各个单位根据自身料仓遇到的问题,采取临时的局部应急措施。在某种程度上解决了现场临时的问题,但对于整个行业来说,并没有形成一套完整的解决方案。
其二是:被动性,以上料仓事故处理的所有方法,全部是因料仓形成既有事故后开展实施的,没有前瞻性和预见性。
中矿冶金科技有限公司研发团队通过现场大量的调研总结,就是要在行业内形成一套解决料仓难题的产品体系,从根本上解决料仓所遇到的种种难题,而不是拘泥于某一个料仓的问题。
中矿冶金科技有限公司研发的料仓智能运行系统具有显著的自身特征:
其一是:综合性,根据料仓容易发生堵仓、窜仓、蓬仓等事故,综合治理,标本兼治,形成一套完整的产品体系。
其二是:主动性,从原料来源入手,在原料入仓之前,对原料进行有效处理,防止料仓事故发生。
其三是:智能性,在料仓运行系统中置入图像智能识别技术,通过软件建立数据库,使系统具有自学习能力,替代人工监测。
八、项目重大意义
目前现场运行的料仓数量庞大,事故发生非常频繁,给生产及人身安全造成重大损失,中矿冶金科技有限公司研发的料仓智能运行系统产生了良好的经济价值和社会价值,具有很强的推广应用价值。
具体如下:
1、确保原料仓的正常运转;
2、避免料仓灾害事故的发生;
3、提高现场工作人员的管理水平;
4、为行业树立新的标杆及标准。
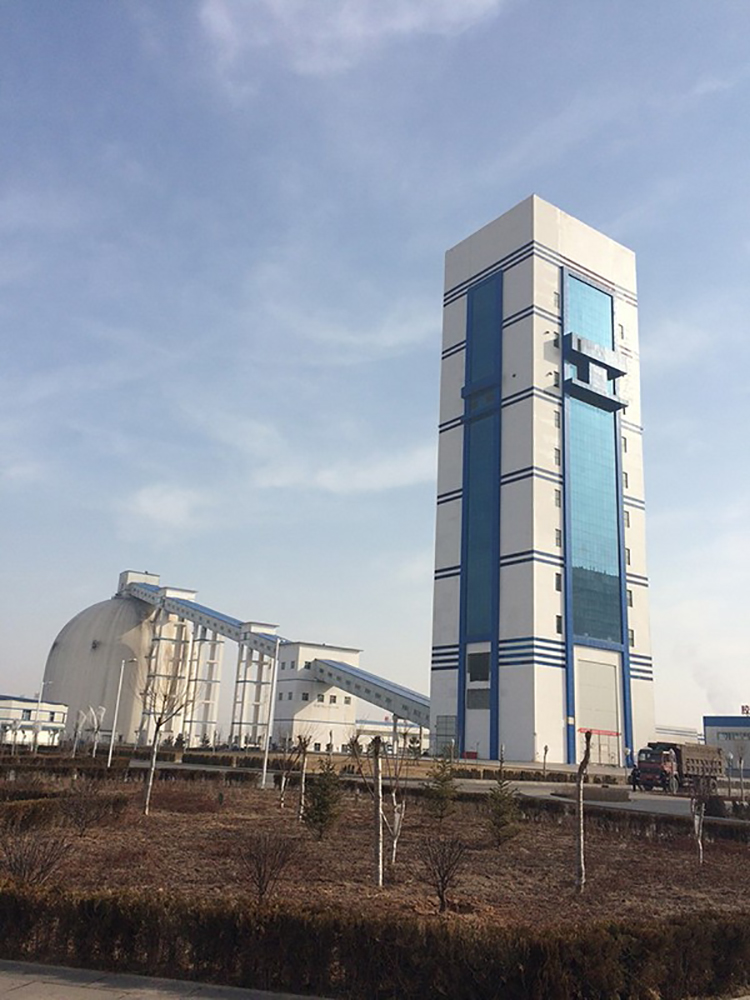